GUIDE - WHY DOES MY CLUTCH ENGAGE AT IDLE?
One of the things we are constantly asked is why a particular customer's dry centrifugal clutch has failed. We've decided to write an informative guide to help understand how Dry Centrifugal Clutches work
Learn how to install a dry clutch by CLICKING HERE
Learn how to service and repair a CPR SR clutch by CLICKING HERE
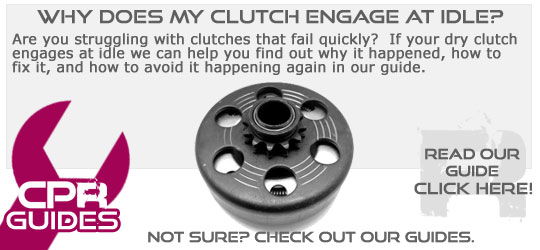
CONTENTS
1. How does the Dry Centrifugal Clutch work?
2. What causes failure in dry clutch systems?
3. What is the mimimum speed I need to travel at to stop my clutch from failing?
1. HOW DOES THE CPR SR CLUTCH WORK?
Basic dry centrifugal clutches run a very simple method of power transfer. This makes them incredibly inexpensilve - one of their major pros. Both our popular entry level stock clutch (such as the CLC3512) and our GT clutch (such as the CGT3512) both emply this technology slightly differently, but the concepts are the same.
The clutch comprises of three main pieces:
- The outer drum (and drive sprocket)
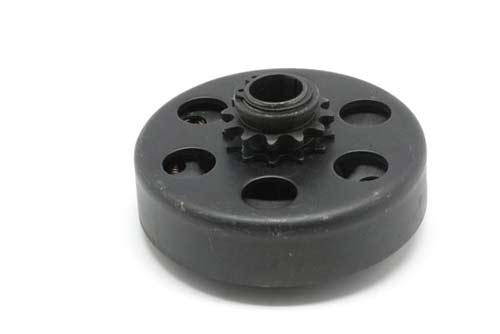
- CLC3512.jpg (7.36 KiB) Viewed 3241 times
- The friction material & arrestor spring(s)
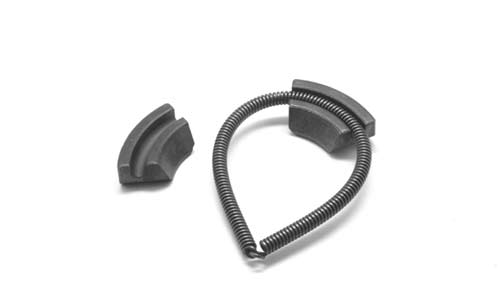
- InnerB.jpg (6.68 KiB) Viewed 3240 times
- The transmission plate & central shaft. (central shaft not shown. Picture below shows friction material and spring installed)

- Inner.jpg (15.72 KiB) Viewed 3240 times
In the picture above you can see the friction material installed onto the transmission plate. You can see the transmission plate splines in the centre of the plate. The central shaft (not shown) slots into these splines and slides onto the crankshaft of the engine. It rotates with the engine because it is keyed and the key slots into the keyway on the crankshaft.
The drum sits over this material and is large enough so that the material does not contact the drum when it is fitted. You can rotate the drum freely when the unit is assembled as the friction material does not contact the drum.
As the speed of the crankshaft rotation increases (RPM increases) there is more and more centrifugal force on the friction material.
The spring holds them together in a tight circle and they do not touch the drum.
As the force pushing the friction material away from the centre increases to a point that it is greater than the force applied by the spring, the friction material starts to move outwards and contacts with the drum.
2. WHAT CAUSES THE CLUTCH TO FAIL?
This begins to happen somewhere between 1500rpm and 1800rpm on the standard DRY CLUTCHES. At this point, the drum is still slipping on the friction material because the amount of force is not great enough to overcome the friction from the back wheels. The more weight, the more friction. When the drum slips, it creates heat. This is the cause of immediate idle on a Dry Centrifugal Clutch. Limiting the slip of the drum is critical to ensuring the clutch does not fail.
NOTE: DRY CLUTCHES SHOULD NOT BE IDLED!
ONE MORE IMPORTANT THING TO NOTE IS THAT AFTER THE FIRST USE, SOME HEAT WILL INEVITABLY BE TRANSFERRED TO THE SPRING AND IT WILL STRETCH SLIGHTLY. FROM THIS POINT ON, AT IDLE, THE CLUTCH WILL SLOWLY BEGIN TO ENGAGE AT IDLE SPEED - THE HIGHER THE IDLE SPEED, THE MORE THE ENGAGEMENT WHICH WILL ACCELERATE WEAR.
At 2000rpm the friction material has so much centrifugal force applied to it that the spring can no longer arrest the material and it completely contacts the drum. This is considered it's FULLY ENGAGED rpm. Power is now transmitted directly through the chain to the rear drive sprocket and no further heat is created.
3. WHAT IS THE MINIMUM SPEED I NEED TO TRAVEL TO STOP CLUTCH FAILURE?
It's important to note that if you are running the clutch at less than 2000rpm, it will be slipping. This willl cause the heat that will stretch the spring. If you ensure that the vehicle is always travelling at a minimum of the speed required to engage the clutch, then the clutch will last for a long long time.
You will need to know the following to determine your minimum speed:
1. The rolling diameter of your tyres in inches.
This measurement is from the ground, to the top of the tyre. If you measure in mm then divide by 25.4 to get inches. If you measure in cm then divide by 2.54 to get inches.
If your tyre is marked in the same convention as most go kart tyres, it will have the overall diameter listed as part of that number designation. For example, a 11-7.10-5 tyre has an 11 inch over-all diameter. And a 13x6.00-5 tyre will have a 13 inch overall (rolling) diameter. It is important to note that you may need to measure anyway if you want to be accurate so that you cover additonal rolling diameter created by inflating the tyre.
2. The transmission ratio.
This is the static ratio of the drive axle sprocket (rear axle sprocket in go karts) to the front (clutch) sprocket. Calculate the ratio by dividing the drive axle sprocket (rear axle sprocket) by the front (clutch) sprocket.
If you are running a reduction jackshaft, reduction box, or torque converter you will need to use it's ratio. This is entered into the Differential Ratio section. If you are just runnign a simple dry clutch and rear sprocket then this is just left as 1:1. If you were using a torque converter you would generally use 2.7 for this value.
EXAMPLE 1 - Racing Go Kart with standard senior slick rear tyres, a 60T rear axle sprocket and a 12T clutch.
For this example, we'll explore calculating the minimum speed required to engage a clutch fully on a standard racing go kart running standard senior slicks.
1. Rolling Diameter of the Tyres
We're using 11x7.10-5 tyres so we'll use 11 for this value
2. Transmission Ratio.
We're using a 60T rear axle sprocket, and a 12T front clutch sprocket = 60/12 = 5:1
When we enter this into the calculator we receive this output:
So the calculator tells us that when we are driving at any speed lower than 21 KPH we are damaging our clutch.
Increasing the rear sprocket size will help with this value, for example if we increase our sprocket size to 73T we can reduce the minimum speed to 17kph.
To reduce further, we would need to use a reduction jackshaft, or a torque converter.
EXAMPLE 2 - Racing Go Kart with standard senior slick rear tyres, a 60T rear axle sprocket and a 12T clutch AND TORQUE CONVERTER.
By utilising a torque converter, we can reduce the minimum speed to a crawl but without affecting the maximum speed. This makes the torque converter system far more practical for off-road karts and kids karts where slow speeds are going to be common while the driver is learning.
1. Rolling Diameter of the Tyres
We're using 11x7.10-5 tyres so we'll use 11 for this value
2. Transmission Ratio.
3. Differential Ratio.
The initial differential ratio is 2.7:1
.jpg)